In addition to vehicle tires, there are many other sources of scrap rubber, like shoe soles, gumboots, rubber pipes, conveyor belts, rubber cables, telephone and submarine cables, rubber gloves. These waste rubber sources are not degrading quickly and will take up a lot of space in landfills and other areas for decades. Hence, increasingly businesses and organizations, who produce or collect rubber waste are preferring to invest in rubber waste recycling plant which will process the waste rubber and convert it into valuable materials which can be sold to make a good profit or used as fuel for the equipment.
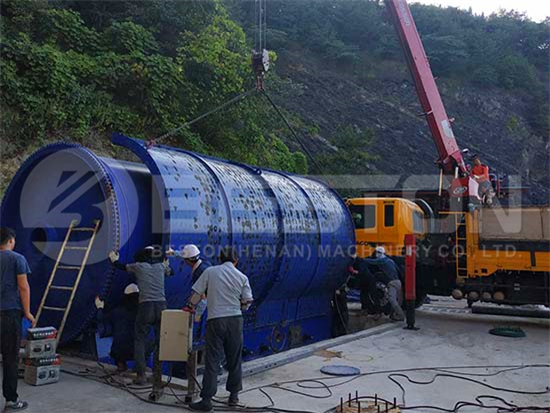
Rubber Oil Plant in Korea
The rubber recycling plant is available in different capacities based on the amount of raw material available and initial investment which the buyer can afford. The smaller plants are of batch type, and they will be used only for some hours a day, based on the raw material available. These equipment are suitable for buyers who can invest less, and the profit is also lower since the furnace has to be heated every time the machine is started. For higher profit, a semi-continuous or continuous machine is preferred, though the investment is higher and the buyer has to ensure a continuous supply of raw material.
The scrap rubber can be loaded in the machine automatically or manually. Manual loading is cheaper, while automatic loading is faster and safer. The rubber is then crushed or converted into smaller size pieces for better processing. For converting rubber into oil, the rubber undergoes the process of pyrolysis. In this process, the rubber is heated at a high temperature in the absence of oxygen in a furnace, due to which the chemical bonds in the rubber will break and the chemical composition of the scrap rubber will change. It is advisable to keep the pyrolysis machine heated before loading the rubber.
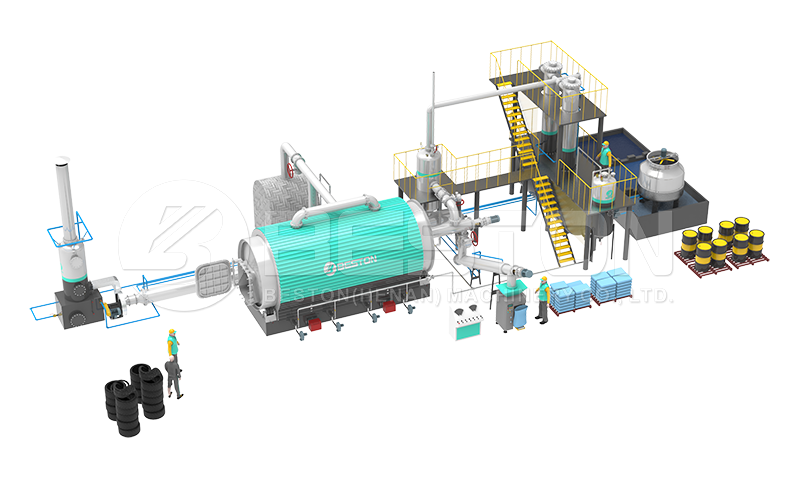
Layout of Pyrolysis Plant
Fuel Oil
A catalyst with different elements is used to enhance the processing and reduce sulphur content. After a temperature of 100 degree centigrade is reached, fuel gas is produced. As the temperature is increased various fuel gases are produced. Dust collectors and cyclone are used to remove the dust and other impurities in the oil. These gases are then passed through a manifold and the gas will liquefy to form oil. This fuel oil is then sold to buyers, used in diesel generators to enhance combustion, used a fuel for the furnace, or distilled to convert it into diesel and gasoline.
Carbon Black and Gas
The other raw material which is produced from the pyrolysis of rubber is carbon black and fuel oil. The carbon black is used for making master batches for paint and other coloring material. It can be also processed into coal or sold. The combustible gas which is produced is used for heating the furnace or is sold. So the process of pyrolysis of scrap rubber is very environmentally friendly since there is no waste material generated, which have to be disposed. All the products can be sold for a profit by the machine owner, or used for the processing of waste rubber.

Carbon Black
Raw Material and Oil Output
It should be noted that the amount of oil produced from waste rubber, depends to a large extent on the type of waste rubber which is being used. When the rubber is made into different products, the additives and rubber composition will vary, and when these products are scrapped, processed in a furnace, the products which are obtained will differ to a great extent. For example, oil obtained from submarine cables will be 75% by weight, while the oil yield when shoe soles are used will be 30% or slightly more. Hence the buyer of the machinery should try to find suitable rubber scrap sources.
Installation & Maintenance
For a daily capacity of up to 10 tonnes, batch type rotary pyrolysis plants are usually used. The furnace diameter and length will increase depending on their capacity. Different types of raw material like charcoal, wood, combustible gas, oil can be used for heating the furnace depending on the availability. Water cooling is used for cooling all the finished products. Typically each machine will last for five to eight years. The machine manufacturer will install the machine at the customers factory, and also train the staff. They will also periodically inspect the machine, and ensure that there is no problem.
Conclusion
Based on the above information, investing in rubber recycling machinery can be profitable. More information can be found: https://beston.co.za/.